Create a new generation of robots with digital twins
#The status of robots has never been higher as manufacturers and warehousers turn to robotics to respond to market pressures that overwhelm traditional technologies and practices. However, these robots are not the machines of the past, which were physically intimidating systems with limited intelligence and mobility that did not interact well with humans. Today's robots are flexible systems with significantly improved intelligence and perception capabilities that can perform complex and delicate tasks while working together with humans.
To build the next generation of robots, engineers will need technologies and practices that provide greater visibility, flexibility and efficiency. To cope with unprecedented levels of complexity, all engineering disciplines must collaborate like never before, leveraging data-rich environments.
This is where digital twins come in.
With the enhanced modeling and simulation capabilities brought by digital twin technology, engineers can better design, develop, deploy and monitor robots in manufacturing and warehouse applications.
Erin Rapacki, senior product marketing manager for NVIDIA Robotics, said: “We now have the technology needed to create real-world digital twins. Digital twin simulations of manufacturing facilities and warehousing and logistics facilities will allow operating companies to optimize efficiency and significantly To reduce costs and waste."
Rapacki pointed out that to perform these complex simulations, users need to simulate all aspects of the digital twin, including robots, sensors, people, and other assets such as conveyor belts.
He said: "Robot developers need to be able to rehearse the complete software stack, including safety systems, thousands of times in a simulated environment before deploying to the real world."
Implementation Painless Design
When developing a new industrial robot system, the development team hopes to quickly try out different design and control concepts and lock in the final product requirements. With access to a digital model of the physical system, there is a virtual testbed to run iterative designs at lower cost and shorter lead times than creating physical prototypes each time. This allows design engineers to cast their net further, investing time and resources to explore concepts and methods that traditional approaches cannot support.
Chris Harduwar, vice president of strategic solutions at Maplesoft, said: "This broader analysis capability allows us to consider the challenges that previously took too long to evaluate when creating new innovative uses. An extreme case of discounting. Because the digital model is synchronized with operational data, a comprehensive digital twin is formed that can respond like a physical asset. This digital twin can also be used as a flexible platform, using to validate control strategies and production line plan updates, resulting in a safer, more robust product.”
However, to reap the full rewards promised by digital twin technology, development teams must consider the big picture, including all the Subject. Digital twins and simulations can also help.
Rapacki said: "A digital twin of a manufacturing facility or warehouse logistics facility can establish digital connections between all activities in the workspace and integrate traffic, obstacles, optimal routes, updated pickups/ Changes such as delivery points are communicated to the robotic device."
For example, a mobile robot can more easily blend with the real environment when it uses the same simulated environment as the facility's digital twin. The robot’s sensor stack leverages actual digital twins at the customer’s site for robot perception training and testing. Customer sites also provide synthetic data for computer vision training, and vSLAM (Visual Simultaneous Localization and Mapping) on the robot helps the robot navigate based on updated facility models.
Using offline programming
The complexity of robot programming and the high cost of debugging robot systems in warehouses or production workshops make modeling and simulation that supports digital twins a complex robot application design and deployment and an important part of maintenance. Once the robot and associated processes are designed and verified, engineers can use modeling and simulation tools to perform offline programming.
Supports modeling and simulation of digital twins, allowing design teams to develop and test code before the complete physical system is complete, saving time by allowing code programming and physical system construction to be completed in parallel.
Roberta Tanzariello, head of robotics and digital tooling platforms at Rockwell Automation, said: “The results ensure optimized cycle times and collision-free trajectories, and the advanced robot simulation software enables the deployment of challenging robots with offline robot programming. applications such as welding, drilling and cutting. Users can then add details to create complete programs offline."
Once the initial digital model is created and tuned using the first pass nominal data, it can be Integrated with control system development tools.
For manufacturing automation, controls engineers can prepare a virtual [programmable logic controller (PLC)] and use the signals as inputs to a digital twin that engineers can verify and simulate, Harduwar said. An environment that physically responds to new code."
Offline validation is valuable for preliminary integration testing of systems operating in hazardous work environments or where code errors could cause harm to the robotic system or operator. of. This way, testing failure conditions is safer and can be done more quickly in a virtual environment.
On existing robotic systems, engineers can investigate issues through online simulation and use digital twins to represent the production environment in the same way digital twins evaluate how code updates are performed.
We are seeing digital twins being used to resolve anomalies reported by customers who have discovered issues with the hardware running their sites, and once the root cause is identified, programming changes can be applied Use this model to validate expected results before running them against a real-time system, significantly reducing system downtime and preventing the costly impact of coding errors."
Expanding the possibilities for AI training
Numbers Twin technology also helps train AI algorithms, and these mechanisms allow robots to perform complex applications in production and warehouse environments.
Prior to this, algorithm training was often hampered by a lack of training data. Often, robotics development teams find problems with non-existent training data, which greatly limits the applications in which algorithms can be trained to perform.
The challenge of training algorithms is further complicated by requiring robots to perform a large number of unique applications, exacerbating the problem of training data.
However, digital twin technology now provides a way to train AI algorithms to handle a greater number and type of use cases. Digital twins can generate simulation data and test new functions, quickly completing large quantities of configurations and designs. The data generated by these simulations can then be used to train AI models to adapt to a wider range of real-world conditions and test scenarios.
Alex Greenberg, director of advanced robot simulation at Siemens Digital Industries Software, said: "Using synthetic data generated by digital twin simulation allows AI algorithms to learn and adapt to different conditions and changes in the physical world. This approach helps To reduce the risk of potential problems in the real world."
Another example is in the field of 3D computer vision (i.e., machine perception and sensor fusion). 3D computer vision is crucial for robot manipulation and sensing the distance of objects. .
Rapacki said: "Object distance is critical to the robot's ability to manipulate, grasp or avoid objects. The robot must understand how far away the object is. Digital twins provide endless scenarios with geometric characteristics, 3D robot perception pipelines can use these scenarios to train capabilities such as collision avoidance and grasping."
There is also a technology called "reinforcement learning" that uses digital twins to solve the most complex problems, further pushing reached the limits of artificial intelligence technology. The technology allows algorithms to learn how to perform tasks through trial and error in simulations, a process that is not possible in the real world.
Overcoming Debugging Barriers
Another area where digital twin modeling and simulation capabilities can be leveraged is in robotic system debugging and deployment.
While these processes face obstacles, the main bottleneck that engineers must contend with is the increased access to physical systems required by those who must verify robot functionality.
Unfortunately, building and running physical systems is expensive and often impractical, so an alternative is needed, and this is where the virtual debugging capabilities of digital twin technology come into play.
This process—using a representative customer environment as a digital twin in a simulation—addresses these challenges while increasing efficiency.
Virtual debugging capabilities enable engineers to connect digital twins to control systems (such as PLCs) and other external devices to test, refine and optimize mechanical, electrical and logical designs before any hardware is available without stopping production .
Hardware loop simulation can be performed as part of the virtual debugging process. Wherein, different types of equipment and systems can be combined in a complex system layout to provide the development team with a holistic view of the robot's performance in the operating environment.
The PLC is connected to the robot and the complete deployment is considered in a detailed simulation that includes factors such as gravity, force and torque to determine the size of the application based on the required cycle time. In this case, the simulation function tests real control inputs from the PLC and feedback from the simulation model.
Engineers are often able to find and correct programming errors and mechanical interference issues through the virtual debugging process, which also verifies dynamic areas and robot working ranges to ensure safe operations.
Maplesoft’s Harduwar said: “Using simulation software in this way, robotics engineers can generate different virtual prototypes more quickly than building a single physical system. Testing the digital model under various operating conditions performance, and is also easier than setting up multiple test spaces in a warehouse."
Support for digital twin virtual debugging capabilities can help robotics development teams achieve a high level of accuracy, providing methods that can not only verify Individual devices and subsystems, and how well all components work together can also be verified.
Simulation capabilities allow robotics engineering teams to be as close to perfect as possible in validating edge cases and performing bug fixes, merging code, and managing behavior trees and deployment integrations, Rapacki said. “This system-level verification—especially Code updates – speeding up deployment time and significantly improving robot quality.”
When digital twins enter the field
Once the robotics development team has the digital twin ready, it can transfer simulations Expand applications beyond the design and initial commissioning phases. If real-time operational data is available from sensors or can be inferred from historical data, then the development team can enhance the digital twin to enhance the physical robotic system it represents over time. This can support the optimization of performance by adjusting controllable parameters to maximize throughput and find ways to reduce operational wear and tear to drive business results.
"The performance of robots can be evaluated and tested based on real-life behavior observed during operation, and digital twin simulations can be used to support predictive and prescriptive measures to improve performance or evaluate alternatives to potential problems solution,” said Mike Rouman, senior marketing manager for digital manufacturing at Siemens Digital Industries Software.
For robotic assets that need to respond to changing environments or interact with other machines, digital twins can serve as an ideal operational case, allowing designers to detect anomalies and consider adjustments to production, simplifying the process product improvements and processes to be able to make adjustments when performance parameters fluctuate.
In the industry today, digital twin technology is being used to troubleshoot operational hardware because the model provides context for the problem, allowing designers to troubleshoot without taking the affected system offline. Any remediation and code change actions. Thanks to the good quality of sensor data and the reduction in simulation run times, digital twins allow the system to be studied from a more advantageous point than standard fixed-time simulations.
Harduwar said: "The challenge going forward will be to develop fast and efficient digital twins in a wider range of environments and train more engineers to learn to use and apply the tools that support these digital transformation technologies."
The above is the detailed content of Create a new generation of robots with digital twins. For more information, please follow other related articles on the PHP Chinese website!

Hot AI Tools

Undresser.AI Undress
AI-powered app for creating realistic nude photos

AI Clothes Remover
Online AI tool for removing clothes from photos.

Undress AI Tool
Undress images for free

Clothoff.io
AI clothes remover

Video Face Swap
Swap faces in any video effortlessly with our completely free AI face swap tool!

Hot Article

Hot Tools

Notepad++7.3.1
Easy-to-use and free code editor

SublimeText3 Chinese version
Chinese version, very easy to use

Zend Studio 13.0.1
Powerful PHP integrated development environment

Dreamweaver CS6
Visual web development tools

SublimeText3 Mac version
God-level code editing software (SublimeText3)

Hot Topics

The humanoid robot Ameca has been upgraded to the second generation! Recently, at the World Mobile Communications Conference MWC2024, the world's most advanced robot Ameca appeared again. Around the venue, Ameca attracted a large number of spectators. With the blessing of GPT-4, Ameca can respond to various problems in real time. "Let's have a dance." When asked if she had emotions, Ameca responded with a series of facial expressions that looked very lifelike. Just a few days ago, EngineeredArts, the British robotics company behind Ameca, just demonstrated the team’s latest development results. In the video, the robot Ameca has visual capabilities and can see and describe the entire room and specific objects. The most amazing thing is that she can also
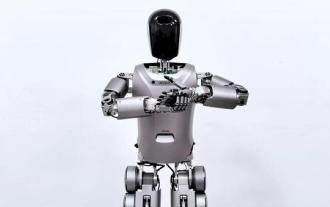
Editor of Machine Power Report: Wu Xin The domestic version of the humanoid robot + large model team completed the operation task of complex flexible materials such as folding clothes for the first time. With the unveiling of Figure01, which integrates OpenAI's multi-modal large model, the related progress of domestic peers has been attracting attention. Just yesterday, UBTECH, China's "number one humanoid robot stock", released the first demo of the humanoid robot WalkerS that is deeply integrated with Baidu Wenxin's large model, showing some interesting new features. Now, WalkerS, blessed by Baidu Wenxin’s large model capabilities, looks like this. Like Figure01, WalkerS does not move around, but stands behind a desk to complete a series of tasks. It can follow human commands and fold clothes
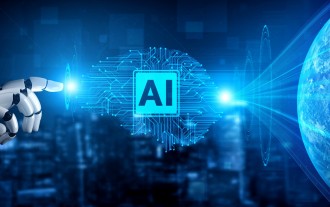
In the field of industrial automation technology, there are two recent hot spots that are difficult to ignore: artificial intelligence (AI) and Nvidia. Don’t change the meaning of the original content, fine-tune the content, rewrite the content, don’t continue: “Not only that, the two are closely related, because Nvidia is expanding beyond just its original graphics processing units (GPUs). The technology extends to the field of digital twins and is closely connected to emerging AI technologies. "Recently, NVIDIA has reached cooperation with many industrial companies, including leading industrial automation companies such as Aveva, Rockwell Automation, Siemens and Schneider Electric, as well as Teradyne Robotics and its MiR and Universal Robots companies. Recently,Nvidiahascoll
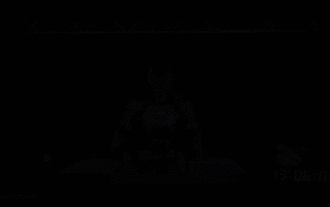
This week, FigureAI, a robotics company invested by OpenAI, Microsoft, Bezos, and Nvidia, announced that it has received nearly $700 million in financing and plans to develop a humanoid robot that can walk independently within the next year. And Tesla’s Optimus Prime has repeatedly received good news. No one doubts that this year will be the year when humanoid robots explode. SanctuaryAI, a Canadian-based robotics company, recently released a new humanoid robot, Phoenix. Officials claim that it can complete many tasks autonomously at the same speed as humans. Pheonix, the world's first robot that can autonomously complete tasks at human speeds, can gently grab, move and elegantly place each object to its left and right sides. It can autonomously identify objects
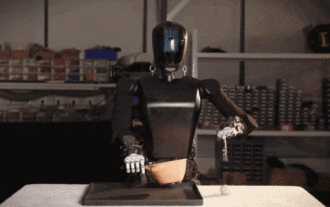
In the blink of an eye, robots have learned to do magic? It was seen that it first picked up the water spoon on the table and proved to the audience that there was nothing in it... Then it put the egg-like object in its hand, then put the water spoon back on the table and started to "cast a spell"... …Just when it picked up the water spoon again, a miracle happened. The egg that was originally put in disappeared, and the thing that jumped out turned into a basketball... Let’s look at the continuous actions again: △ This animation shows a set of actions at 2x speed, and it flows smoothly. Only by watching the video repeatedly at 0.5x speed can it be understood. Finally, I discovered the clues: if my hand speed were faster, I might be able to hide it from the enemy. Some netizens lamented that the robot’s magic skills were even higher than their own: Mag was the one who performed this magic for us.
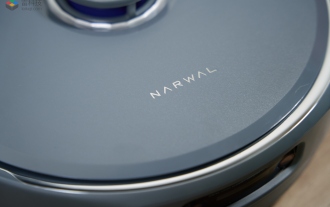
Sweeping and mopping robots are one of the most popular smart home appliances among consumers in recent years. The convenience of operation it brings, or even the need for no operation, allows lazy people to free their hands, allowing consumers to "liberate" from daily housework and spend more time on the things they like. Improved quality of life in disguised form. Riding on this craze, almost all home appliance brands on the market are making their own sweeping and mopping robots, making the entire sweeping and mopping robot market very lively. However, the rapid expansion of the market will inevitably bring about a hidden danger: many manufacturers will use the tactics of sea of machines to quickly occupy more market share, resulting in many new products without any upgrade points. It is also said that they are "matryoshka" models. Not an exaggeration. However, not all sweeping and mopping robots are
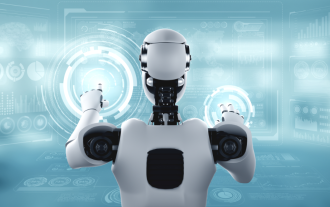
The following 10 humanoid robots are shaping our future: 1. ASIMO: Developed by Honda, ASIMO is one of the most well-known humanoid robots. Standing 4 feet tall and weighing 119 pounds, ASIMO is equipped with advanced sensors and artificial intelligence capabilities that allow it to navigate complex environments and interact with humans. ASIMO's versatility makes it suitable for a variety of tasks, from assisting people with disabilities to delivering presentations at events. 2. Pepper: Created by Softbank Robotics, Pepper aims to be a social companion for humans. With its expressive face and ability to recognize emotions, Pepper can participate in conversations, help in retail settings, and even provide educational support. Pepper's
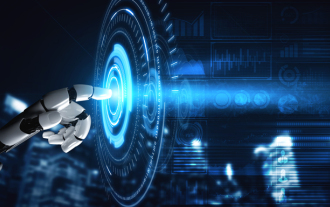
AEC/O (Architecture, Engineering & Construction/Operation) refers to the comprehensive services that provide architectural design, engineering design, construction and operation in the construction industry. In 2024, the AEC/O industry faces changing challenges amid technological advancements. This year is expected to see the integration of advanced technologies, heralding a paradigm shift in design, construction and operations. In response to these changes, industries are redefining work processes, adjusting priorities, and enhancing collaboration to adapt to the needs of a rapidly changing world. The following five major trends in the AEC/O industry will become key themes in 2024, recommending it move towards a more integrated, responsive and sustainable future: integrated supply chain, smart manufacturing
